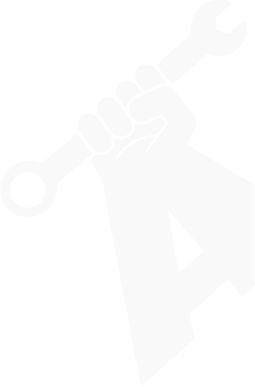
GE Laundry Centre With A Broken Drum Repair
At Max Appliance Repair, we take pride in providing top-notch repair services for all types of appliances, including the recent challenge of repairing an older GE Laundry Centre’s dryer with a dislodged heat deflector. Our well-prepared team assessed the damage and confidently tackled the repair, using their extensive experience effectively.
We turned off the power supply and removed the front panel to access the drum. After lifting the drum out, our technicians replaced the damaged heat deflector with a high-quality, compatible part, ensuring it was secure and properly aligned. We then reassembled the drum, tested the laundry centre for proper heat distribution and drum rotation, and reconnected the power supply. Throughout the process, we kept our client informed and offered tips on avoiding similar issues in the future, ultimately restoring their GE Laundry Centre to full functionality.
Our GE Laundry Centre Repair in Action
At Max Appliance Repair, we take satisfaction in knowing that our customers can rely on us for even the most complex appliance repairs. We are proud to have restored this older GE Laundry Centre to full functionality, ensuring that our client can continue to enjoy its dependable performance. Feel free to contact us whenever you need quality dryer repair services contact us or call us today at (647) 477-0946.
Some More Common Issues With GE Laundry Centres
GE Laundry Centres are renowned for their sophisticated capabilities and exceptional performance. Nonetheless, as with any electronic appliance, they may encounter occasional issues. Below, we explore five prevalent concerns that may arise with GE Laundry Centres:
Inadequate drying or extended drying times:
One common issue in GE Laundry Centres is that clothes may not dry properly or take longer than usual to dry. This could be due to a clogged lint filter, obstructed air vents, or a malfunctioning heating element.
Washer not draining or spinning:
Another frequent problem is the washer failing to drain or spin effectively. This can be caused by a clogged drain pump, a worn-out drive belt, or a faulty lid switch.
Unusual noises during operation:
GE Laundry Centres may sometimes produce strange noises while running. These noises can result from worn or damaged drum bearings, a loose drive belt or foreign objects caught between the drum and the laundry centre’s housing.
Leaking water:
Water leaks are also common in GE Laundry Centres. Leaks can occur due to a damaged door seal, a cracked or loose hose, or an issue with the water inlet valve.
Control panel issues or error codes:
Users may encounter issues with the control panel or see error codes displayed on the screen. These problems can stem from a faulty control board, a damaged keypad, or issues with the wiring or connections within the laundry centre.
Licensed & Experienced
Warranty on Parts & Labour
100% Customer Satisfaction
Award Winning Support
24/7 Emergency Services
Common Error Codes For GE Laundry Centres
Here are some common error codes found in GE Laundry Centres Made After The Year 2011.
These error codes typically indicate a problem with the washer’s drain system, such as a clogged pump filter or a slow-draining pump. You may need to clean the filter or check the drain pump for blockages.
These codes signal an issue with the door lock or door switch assembly. The washer may not be able to detect whether the door is properly closed, which prevents it from starting a cycle. Inspecting the door lock or switch for damage and replacing it if necessary may resolve the issue.
This code points to a problem with the current sensor on the dryer’s motor. It may mean that the sensor is faulty, or there may be an issue with the wiring. Troubleshooting the sensor and checking the wiring connections can help identify the root cause.
These error codes are associated with heater-related problems in the dryer. E61 indicates that the heater is not receiving sufficient power, while E62 means that the heater is receiving too much power. In either case, checking the wiring and the heater itself may help identify the issue.
These codes suggest an imbalance in the washer’s load during the spin cycle. The washer may have difficulty balancing the load, leading to excessive vibrations and noise. Rearranging the laundry items for better distribution or reducing the size of the load can help address this problem.
Certified Technicians
Do you need help?
Get a Free Quote
To schedule your appointment or get an estimate give us a call or fill in the form
Toronto & GTA
(647) 477-0946
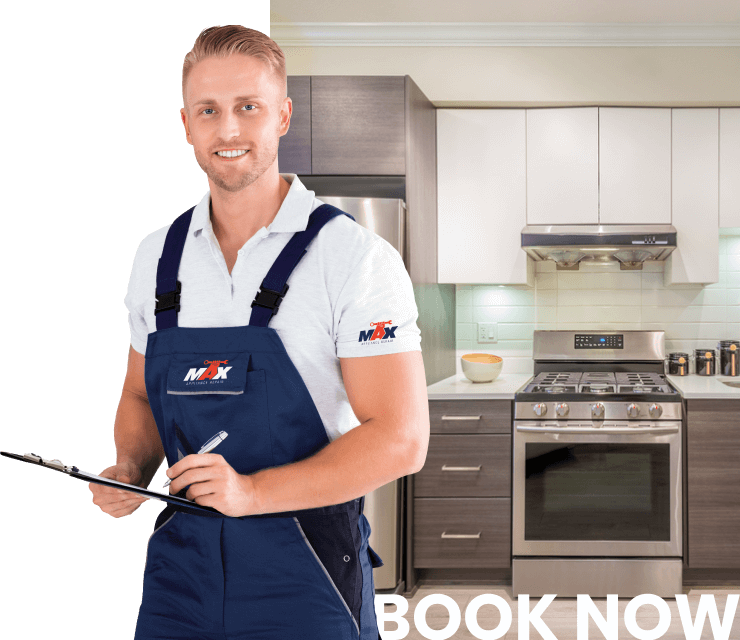
Frequently Asked Questions About GE Laundry Centres
It is recommended to clean the lint filter after every drying cycle to maintain optimal performance and prevent potential fire hazards.
This could be due to a clogged drain pump, a kinked or damaged drain hose, or a faulty lid switch. Check for any obstructions and inspect the relevant components.
Unusual noises can result from worn drum bearings, a loose drive belt, or foreign objects caught between the drum and the appliance’s housing. Inspect and address these issues as needed.
Overloading the washer, using the wrong cycle settings, or an imbalanced load can cause clothes to become wrinkled or tangled. Ensure the washer is loaded correctly and choose appropriate settings for the fabric type.
To reset the appliance, unplug it from the power source, wait for 30 seconds, and then plug it back in. This may clear the error code and reset the system.
A non-functioning heating element, a faulty thermostat, or a blown thermal fuse could be the cause. Check these components and replace them if necessary.
GE Laundry Centres are designed as a single units with a stacked washer and dryer. However, if you have separate GE washer and dryer units, you may be able to use a stacking kit compatible with your specific models.